Four Supply Chain Challenges Facing Retailers
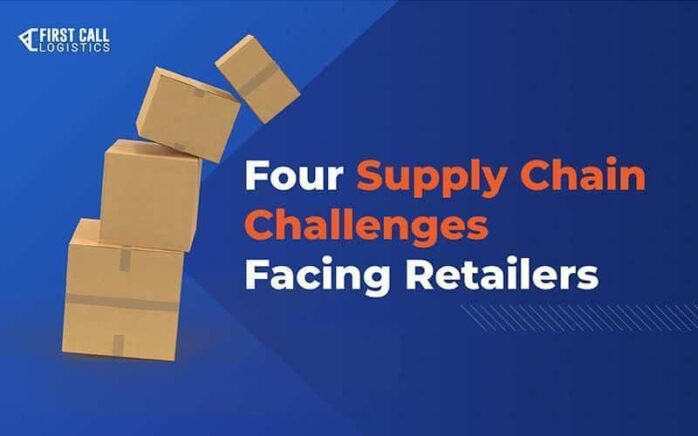
The past three years have exposed a host of pain points within retail supply chain management. Increasingly limited resources, new tech demands and consumer expectations that often seem contradictory can make logistics an unnecessary headache for businesses caught unprepared for the next inevitable disruption.
For retail brands struggling to build a more resilient supply chain, a third-party logistics partner can prove an elegant solution. Here are four key supply chain challenges a 3PL can help retailers keep in check:
1. Shifts in Consumer Demand and Expectations
Consumers have grown to expect fast shipping — in fact, nearly 90% of U.S. online shoppers expect free two- to three-day shipping but changing consumer values are also driving significant sustainability efforts across most industries. Research shows roughly 62 percent of Generation Z and Millennial participants say they prefer to buy from sustainable brands.
As a growing number of online shoppers show loyalty to brands with eco-friendly practices, companies are left trying to balance sustainable supply chain management with ultra-efficient shipping speeds. Logistics experts are attacking this particular challenge on two key fronts:
- Exploring sustainable materials and packaging options. Utilizing more recyclable or reusable packaging is among the most common solutions companies identify in their efforts to become carbon-neutral (or even better, carbon negative).
- Optimizing inventory to reduce waste. Advanced industry tech allows companies to better plan supply chains around seasonal trends and shifts in demand. That means less storage space and fewer resources dedicated to moving unsold products, and ultimately more efficient operations.
2. Limited Drivers and Warehouse Space
As you might have read, logistics companies are currently short around 80,000 truck drivers in the U.S. alone – a figure expected to double by 2030. This presents major problems for retailers looking to expand the volume of products they can reasonably move, store and sell.
Speaking of storage, increasing numbers of retailers now also face the prospect of overflowing warehouses. As the cost of real estate skyrockets, demand for available warehousing space grows exponentially – with fewer items on-hand in centrally-located storage facilities, companies already relying heavily on complex supply chains now have even less margin for error.
Here are three ways retailers are easing the burdens of limited drivers and storage space:
- Automating inventory management processes. With more advanced tools and the ability to predict supply and demand patterns, retailers can gain a more accurate picture of their inventory and better manage delivery of just-in-time items.
- Creating flexible storage. Repurposing some store space as fulfillment space can help with the growing volume of e-commerce orders and ease the lack of warehouse storage.
- Utilize a 3PL’s resources. Maybe this is a bit of a shameless plug, but third-party logistics partners already have drivers, software and warehousing facilities in place for this very purpose!
The right partner with the right tools can help businesses navigate these limited resources and prevent retailers from becoming overwhelmed with shipping, storage and fulfillment responsibilities.
3. Catastrophic Weather Events
While it’s no secret that climate change is impacting the supply chain, many consumers don’t understand just how much of an impact it can make. “Climate Resiliency,” or the ability for a supply chain to withstand catastrophic weather events, is a growing necessity for today’s retailers.
An unprepared team can risk losing up to 35 percent of revenues due to catastrophic weather. This includes physical damages to assets (including facilities), reduced sales, higher reconstruction costs and an increase in the cost of labor. In contrast, a well prepared team might only face the loss of 5 percent of revenues in a similar event.
Here are two ways retailers can be more prepared for weather:
- Dual sourcing. Putting all your logistical eggs in one basket might simplify things for a while, but it also makes your supply chain vulnerable. In the event of a crippling natural disaster, dual sourcing can reduce your overall supply disruption.
- The right insurance plan. Preparing for the proverbial (and literal) rainy day with an insurance plan fit for your business size and needs can help companies quickly recover their losses following catastrophic events.
It’s virtually impossible to predict when the next freak act of nature will impact the supply chain – being prepared with some supply chain diversification and insurance protection can help retailers safeguard operations, just in case.
4. Adopting Data-driven Inventory Management Systems
It’s long been a common practice for retailers to use historical data to predict potential demand, but that is no longer the most efficient way to manage inventory. Instead, tech-savvy retailers are adopting predictive analytics through machine learning and automation. Successful digital transformation is no easy task, but once predictive tools are in place the benefits are enormous:
- Automated purchase orders
- Automated delivery of orders
- Inventory tracking across multiple warehouses
- Multi-channel inventory management
- Reduction of cyber risks
Ultimately, using an automated system helps reduce management costs and better prepares a company’s inventory for coming trends regardless of what past data may suggest. Getting past the initial hurdle of implementation is well worth it in the race to reduce supply chain challenges.
Facing Challenges Head On
With careful planning and proactive implementation, it’s possible for retailers to look to the future and mitigate most challenges before they even appear. Though logistics will always include some measure of risk and uncertainty, understanding the actions we can take now goes a long way toward safeguarding the supply chains of our industry partners.
Simplify your Next Shipment with First Call Logistics
Building and managing cost-efficient supply chains is a full-time job. First Call’s rare combination of in-house assets, expert problem-solving and track record of stellar customer service makes us the 3PL of choice for business partners with a wide range of shipping needs.
More Resources for FCL Shippers:
- Article: What’s Ahead for 3PL Retail Partners in 2023
- Article: The Importance of On-Time In-Full (OTIF) Delivery
- Article: Keeping Up With MABD: What It Is and Best Practices
- Article: 20 Essential Supply Chain KPIs for Your Business to Track
- Article: 20 Warehouse Metrics that Matter Most
- Article: 5 Logistical Challenges Facing the Food and Beverage Industry
- Article: How to Identify Weak Points in Your Supply Chain
- Article: How 3PLs Serve the Seven R’s of Logistics
Get the latest supply chain news and updates directly to your inbox.