Resolving Your Company’s Hidden Logistics Challenges
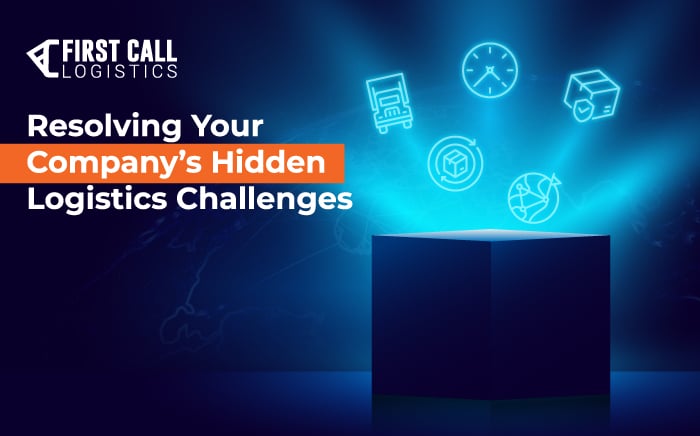
Every disruption along today’s extensive global supply chain creates drag — that’s why it’s so important to seek out problems slowing down your own logistics operation that may have gone long unnoticed, ignored or considered a “necessary evil.”
After years of resolving previously undetected issues for our shipping partners, we’ve noted the tendency for certain areas of the supply chain to attract a disproportionate number of serious disruptions. If you’re not sure where to begin unearthing hidden logistics issues in your supply chain, take a careful look into any of these three areas:
1. Inventory
It’s amazing, the vast amount of logistical problems stemming from inaccurate inventory. Stockouts, overstocking, fulfillment delays and even reduced order fulfillment accuracy can each trace their origins back to deceptively simple inventory errors.
Shippers should regularly evaluate their current inventory management processes, and learn to recognize patterns in stock shortages or other recurring problems to steer clear of future chokepoints.
2. Route Planning
Efficient route planning is key to delivering consistently profitable shipments. Leaving a carrier or individual driver to just wing it once they’re on the road generally leads to increased fuel costs, longer (or missed) delivery times, unhappy customers and tons of unnecessary emissions, which can be especially damaging to companies aiming to adopt a more eco-friendly reputation.
Route planning is also when you’re best-equipped to anticipate inefficiencies that might limit your supply chain and strategize accordingly. Many 3PLs (First Call included) offer route optimization software to facilitate shipment forecasting and devise the fastest, safest route for every delivery — plus, it does this before adverse weather can storm in and derail your best-laid plans.
3. Communication
In logistics, clear communication is the oil that keeps each component of the supply chain firing smoothly. As you can imagine, a lack of communication causes these components to grind against each other or even halt entirely — missed delivery windows, faulty packaging, unsafe temperature ranges and other instances of mishandled freight all owe their presence to a failure to establish clear and consistent contact with the carrier.
Consider the dashboards, apps and other tools at your disposal when connecting directly with suppliers, manufacturers, distributors and retailers — is there a dedicated representative for each stakeholder? How many different channels of communication are in use? What are they, and how do you know if they are working as intended? Learning to measure the quality of your communication will squash the vast majority of disruptions before they can even take shape.
Strategies for Addressing Unseen Logistics Challenges
Identifying long-overlooked or ignored logistics problems isn’t much of a “fix” on its own; shippers and carriers must also prevent these challenges from reappearing.
One of the best strategies for patching up hidden logistics issues is to invest in the right technology (or a collaboration with somebody who already has it integrated).
For example, advanced inventory management systems are now providing businesses with the tools and software to allow for more accurate end-to-end tracking and demand forecasting. It delivers real-time data in order to prevent stockouts and excess inventory. Similarly, GPS tracking and route optimization algorithms are helping to streamline delivery routes, which reduces transportation costs and lowers the company’s overall environmental impact while also building customer loyalty through more efficient deliveries.
Some companies are also implementing collaborative communication platforms as tools to improve coordination, reduce the risk of human errors and achieve better visibility among supply chain partners.
Use a 3PL to Resolve Hidden Logistics Issues
Not many emerging companies have the resources to invest fully in these systems — in fact, most don’t do it all on their own. Instead, they turn to 3PLs like First Call for help. A combination of experience and technological investment on their own dime are major contributing factors to the high demand for 3PL services.
3PLs can both accelerate your business’ ability to scale and save money in the process, as full-time logistics experts remove each of the hidden inefficiencies weighing down the supply chain. If you suspect unseen “drag” might be limiting your supply chain’s effectiveness, reach out to First Call today — we’d love to help!
Simplify your Next Shipment with First Call Logistics
Building and managing cost-efficient supply chains is a full-time job. First Call’s rare combination of in-house assets, expert problem-solving and track record of stellar customer service makes us the 3PL of choice for business partners with a wide range of shipping needs.
More Logistics Resources:
Get the latest supply chain news and updates directly to your inbox.